Digital engineering: How integrating technology with human expertise is unlocking new efficiencies
By Andy Webster, KBR
Digital transformation has become a key driver of progress in the oil and gas industry. This transformation depends on deploying capital in the most cost-effective way. This article explores how the smart use of digital and data is helping navigate the competing demands of affordability and risk.
Rise of digital tech and barriers to overcome
True to Moore’s law of doubling microchip capacity every two years, more powerful, less expensive and less cumbersometechnology keeps coming. The potential this offers the oil and gas industry is largely untapped. While technology has eliminated manual work in blue-collar areas, tedious, low-value white-collar work is proving harder to shift.
The solution is emerging in the form of digital engineers and digital engineering. This goes beyond enterprise software and capability, and beyond information management, in terms of deploying software to achieve a mission. The key to digital engineering lies in deploying roles and individuals focused on business outcomes and that are able to work at the boundary of human and digital tasks.
In response, KBR and other companies operating in the project space are investing in growing digital engineering capabilities.
Cloning data
To drive affordability and lower risk, digital engineering is leveraging the ability to clone or replicate engineering design from one project to another. This isn’t as simple as copying and pasting. Design and engineering assurance requiring significant technical expertise is essential to understand data and make the right judgements. The emergence of model-based systems engineering (MBSE) is enabling engineers to accurately identify when cloning or replication is appropriate.
In a recent project to build a gas processing plant, cloning data from a similar project eliminated the pre-FEED stage completely and reduced the FEED stage, cutting the total project duration by months.
Cloud enabling global collaboration
Technology is enabling collaboration in globally distributed, oil and gas project teams involving dozens of organizations. People who are not used to working together, openly sharing, seeing, using and reacting to common data can be key to project success. The technology itself is simple, but sharing work in real time requires emergent digital engineering skills.
In the pre-FEED stage of one FLNG project, KBR created a cloud-based data room for a team working in London, Perth and Chennai. This underpinned a shared understanding that helped to foster profitable engineering decision-making, cutting pre-FEED stage duration by more than 50%.
Digital twinning
As projects progress, shared data becomes the foundation for a digital twin. For digital engineers the term "digital twin" is akin to the term "maintenance planning" for maintenance engineers. It is not about the software; it is simply where the work happens.
KBR worked with software partner Aveva to develop a digital twin of bp’s new Azeri Central East platform in Azerbaijan. Throughout the project, digital engineers organized huge amounts of data from many sources, helping the project progress ahead of time as the data matured.
Digital engineering helped the digital twin evolve, offering value in the operational phase. It supported critical training and startup activity, removing months from the project duration. A small team continues to maintain the digital twin, enhancing maintenance, safety and productivity.
Conclusion
These recent examples show what is now possible, and where Moore’s law might take us next. For example, the potential with AI is huge, but the technology will only ever be as good as the engineer who wields it. So, as long as the industry keeps investing in the human skills to use digital and data to its full potential, rapid acceleration and risk reduction will be the results.
About the Author
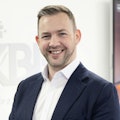
Andy Webster
Andy Webster, who leads KBR’s delivery of proprietary software and capabilities, brings more than 20 years of experience in the energy sector. He is director of digital at KBR and is responsible for leading the company's digital engineering team, which is part of KBR’s wider digital team.