Increased speeds typically lead to increased drilling dysfunctions
Editor's note: This article first appeared in the 2024 Offshore Business Strategies Special Report, which published within the May/June 2024 issue of Offshore magazine.
By Robert Borne, Neo Oiltools
In offshore oil fields, operators continuously seek to drill faster while increasing efficiency and reducing costs. Time is money, and non-productive time (NPT) significantly increases costs. Employing strategies that enable faster drilling speeds while overcoming the inherent challenges encountered when drilling longer and more complex wells can enhance operating efficiency and profitability.
Vibrations encountered downhole can slow the rate of penetration (ROP) and damage critical equipment such as the drillbit or bottomhole assembly (BHA), as well as electronics. That’s why many drillers rely on some form of vibration suppression system (VSS). However, addressing various drilling dysfunctions with individual tools is inefficient, costly and introduces multiple points of failure.
Addressing drilling dysfunctions
Drilling companies and operators routinely contend with axial, lateral and torsional drilling dysfunctions. Axial dysfunctions cause the drill to bounce back vertically, and lateral dysfunctions stem from the BHA hitting the wellbore wall. Torsional dysfunctions involve either low-frequency torsional shocks (stick-slip) where the drill rotates irregularly or high-frequency torsional oscillation that can be particularly destructive for drilling equipment.
There are individual VSS tools that are designed to only address one specific dysfunction. However, putting multiple VSS tools in the BHA to address multiple dysfunctions lengthens it and introduces new potential dysfunctions while also substantially increasing costs. Using a VSS tool that’s engineered to simultaneously mitigate multiple drilling dysfunctions can efficiently minimize any vibration encountered and optimize drilling parameters based on conditions. A cable-design VSS tool can achieve these objectives while improving ROP, reducing the number of trips, preserving equipment and minimizing downtime.
Case study
In one case, a North American operator used the NeoTork cable-design VSS tool to reduce vibrations downhole as well as rerun the directional drilling assembly, rotary steerable system and measurement while drilling on at least two consecutive wells while improving the offset well's ROP. Prior to using a cable-design VSS tool, the operator had experienced substantial tangential vibrations. With a cable-design VSS tool in place, however, both tangential and axial vibrations were significantly reduced, which enabled the operator to attain its goals. With vibrations neutralized, a 10% increase in the drilling rate was achieved to reach 550 ft/hour.
Safeguarding equipment, minimizing NPT
Achieving faster drilling speeds without damaging equipment downhole reduces drilling time and allows assets to be quickly redeployed. Reducing a drilling campaign by one day can save a significant sum, which supports a stronger bottom line.
Increased speeds typically lead to increased drilling dysfunctions. Those dysfunctions can cause catastrophic equipment failure downhole, derailing performance and costs.
Given the need for speed in the field, it is essential to leverage approaches that can unlock new levels of efficiency while safeguarding equipment and minimizing NPT—even in the most challenging operating conditions. It has never been more important to incorporate a strategy to eliminate vibrations as a core component of a drilling project to ensure its success. Technologically advanced drilling enhancements that can mitigate any type of vibration are key.
About the Author
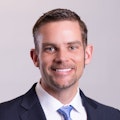
Robert Borne
Robert Borne is CEO and a board director with Neo Oiltools. He has held these positions since March 2024.
Launching his career as a field engineer at Schlumberger Technology Corp., he moved across technical, functional and management roles for 14 years before moving on to leadership roles in both private equity backed and large, publicly traded, energy service companies.