Robin Dupre
Senior Technology Editor
Statoil's ambitious goal of launching a subsea factory in deeper and colder environments by 2020 is on track. Over the course of several years, the company has made several incremental improvements to its existing technology that should make it possible to employ remote-controlled transport of hydrocarbons at any offshore facility.
"The future resources are further from the land, at greater depths and in colder and harsher environments," the company says. "The subsea factory will be vital to realize business opportunities for Statoil in these areas."
By making incremental improvements and tapping into innovative technology from other industries, Statoil and a few service companies are redefining the layout of the subsea sector by creating compact separation facilities on the seabed as a new, low-cost way of producing oil from deepwater and remote locations. While existing subsea production systems usually consist of static components that can remain in place for years, the subsea factory that Statoil is developing involves a standalone subsea production system on the seabed. It will perform tasks that normally are conducted on the surface. For instance, it will employ single- and multi-phase boosting, gas compression, gas-to-liquid and liquid-to-liquid separation, as well as water reinjection.
The recent technological steps in realizing this goal include completion of the first subsea solution for the separation and injection of water and sand from the Tordis wellstream, and the development of the first subsea facility for injection of raw seawater on Tyrihans. Several projects, the company noted, such as the oil-dominated multi-phase transport on Tyrihans and Snohvit's gas condensate transport are a few examples of the major components of the subsea factory development.
One of the biggest hurdles the design has to overcome is bringing power to the factory, which the company is addressing through a step-by-step approach. Statoil started out with 300 KW, then gradually moved up to 11.5 MW on the big compressors, which is a big increase in the power demand for this equipment.
"Along with that, we have qualified the equipment in order to transfer power from shore or from a platform down to the equipment. What we are working on now is instead of just connecting a power cable to each component, like if you have two pumps on, maybe you have one cable to each pump, we are distributing the power subea," stated Statoil's Subsea Technology Chief Engineer Rune Ramberg.
"We have one big power cable brought subsea which will allow the distribution of power to different users," Ramberg continued. "But this initiative is in collaboration with the industry and with other oil and gas companies. We have two big development programs going on now in order to help with realizing this goal."
Statoil partnered with Siemens to help turn subsea factories into a stable and safe power supply by creating the Siemens Subsea Power Grid. It enables subsea processing at a completely different scale than before, said Bjorn Rasch, head of subsea power at Siemens.
Siemens made use of tried and tested air-based components and solutions, which were adapted and qualified for use on the seabed. These components, mainly transformers, switchgears and variable-speed drives (VSDs), together with a comprehensive communication and control system, then were combined to form a complete subsea power grid able to supply and distribute electric power on the seabed.
"Getting components developed in a different environment to function under pressure and in oil have been the most challenging," Rasch noted. "The infrastructure required has been considerable, and we have, in connection with the project, established a unique test lab in Trondheim. This has facilitated testing of areas such as pressure, temperature, current, and voltage."
The project received a go-ahead following a thorough market survey conducted by Siemens, which showed a demand in the market for this type of solution. Chevron was then contacted and informed of the development plans, came on board, and invited Statoil, Petrobras, and ExxonMobil. Seimens led the development, and the four operators contributed to the project with their experience and needs.
"A positive aspect of this collaboration is that the solution is adapted to suit the requirements of all four operators," Rasch said.
Displaying 1/2 Page 1,2Next>
View Article as Single page
About the Author
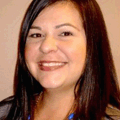
Robin Dupre
Sr. Technology Editor
Robin Dupre is Sr. Technology Editor of Offshore magazine as well as Domestic Editorial Conference Director of three PennWell conferences. Robin has 10 years of experience publishing content for print and online platforms, and she has spent the last 6 years covering the oil and gas industry.