OTC 2025: Four-step mooring integrity management process lowers lifetime costs
By Nick Atallah, Bardex
Mooring integrity management is a rising hot topic in the offshore industry. After decades of equipment installation across the globe, aging systems are in an increasingly variable state of inadequate initial design, poorly maintained equipment and outlasting their original design life. This opens the door to future risk in finding spare parts and knowledgeable field service support. In addition, life-extension programs beyond the mooring systems’ design life are becoming a popular method of approaching finite investment resources.
At this juncture, where additional traditional energy sources will be needed to compensate for the delay in offshore wind, how can the industry support existing infrastructure and ensure future projects don’t meet the same timeworn fate?
A trusted mooring integrity management system consists of a four-action cycle:
- Monitor
- Maintain
- Inspect
- Repair/replace (when necessary)
The industry has moved past the point where monitoring mooring was only asking, “Has the line broken yet?” Now what's currently available includes:
- Mooring loads and movements: Continuous measurement of forces acting on the system;
- Mooring line departure angles: Accurate monitoring to detect abnormal deviations;
- Host offset and dynamics: Tracking the vessel’s motion and its impact on mooring integrity; and
- Host position and heading: Ensuring alignment and proper load distribution.
The industry would benefit from taking to heart the proverb, “An ounce of prevention is worth a pound of cure.” Where some people may see monitoring and maintenance as affecting their quarterly numbers, these actions provide lower lifetime costs and reduce the chance of downtime in the long run.
Next generation of mooring monitoring & inspection
Indirect mooring integrity monitoring provides real-time monitoring and on-demand system status notifications. Using custom-designed and developed predictive software and existing data, changes in mooring performance over time can be predicted, observed and recorded, leading to knowledge about the condition of the mooring system.
In addition, using compact ROVs optimizes inspections in tight spaces and is deployed by a small, expert team. The inspection phase also includes regular checks of onboard equipment during routine operation.
The last phase of the mooring integrity management cycle is repair and replace.
Mooring integrity management cycle
Each of the four stages of mooring integrity management has one thing in common: they plan what is best for the platform’s, and ultimately stakeholders’, future.
Monitoring is the backbone of the mooring system’s health, because what isn’t measured cannot be managed.
Maintenance will happen. Either a company plans for routine maintenance or scrambles when emergency maintenance comes knocking on their door.
Much like maintenance, wear and tear on equipment will happen. Companies should equip themselves with the knowledge gained from monitoring and inspections.
Finally, the replacement stage is integral to extending the usefulness beyond the design life of existing platforms and fixing problems with poorly designed equipment. It also provides invaluable lessons-learned in how not to design mooring equipment. Most importantly, it proves to the industry the importance of selecting systems that are designed from Day 1 to be easily replaced without returning to port.
Conclusion
From people on board, to fragile marine life and even the shareholders, everyone benefits from thinking beyond the next quarterly report and toward a new paradigm in mooring.
Bardex is exhibiting at booth 2343 at the Offshore Technology Conference (OTC) May 5-8 in Houston, Texas. Bardex is also sponsoring "The Four Winds of Connection: Offshore Wind Networking Social" at 5 p.m. CT on Tuesday, May 6, in room 300.
About the Author
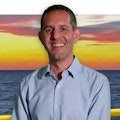
Nick Atallah
Nick Atallah is the director of product development with Bardex. He joined the company in 1998 as a design engineer and is also the former director of engineering.
Over the years, Atallah has helped deliver numerous contributions to the industry such as the off vessel tensioning (OVT) method; a unique, omni-directional, remotely controlled, highly accurate mooring hookup and tensioning method; and mooring tensioning equipment for the largest semisubmersible production platforms in the world.