ROG.e 2024: Better monitoring leads to longer service life for flexible risers
By Domenico Di Giambattista, Baker Hughes
Market conditions in the oil and gas sector are constantly changing, but there is one consistent driver—the need to safely extract as much value as possible from existing assets to get the highest return on investment. As operators look for ways to extend the life of these assets while maintaining safe operations, they also are facing more stringent environmental requirements that raise the bar for performance.
The playing field is changing, and energy technology companies are stepping up their game to develop innovative ways to provide better data, empowering asset owners to make more informed decisions about maintenance and repairs.
Transitioning to new technology
Riser health management is one area where remote, real-time monitoring progress has been particularly impactful. Initial riser inspections relied on cameras and ROVs for periodic visual assessments of subsea assets. However, with the introduction of advanced monitoring technologies that capture integrity data in real time, the industry is moving away from traditional inspection methods and approaching the process in a way that is fundamentally different.
Continuous monitoring is at the heart of this approach. The ability to gather accurate, real-time data across the pipe’s architecture allows operators to identify anomalies as they emerge and make informed decisions about the type and extent of repairs. This way, repairs can be scheduled advantageously to avoid costly operational disruptions.
Historically, when an integrity issue was identified, there was no way to know precisely when it occurred or how long it had existed; so assumptions had to be made based on the results of scheduled inspections. Under these conditions, repairs followed a very conservative plan that would have been unnecessary with more information about the nature and timing of the anomaly.
To work from less conservative parameters while maintaining safety standards, operators need to be able to understand how the riser is performing and the rate at which integrity is being compromised. One reliable way to do this is to implement advanced technologies to gain insights into riser health.
Applying new tools
Today, electronic breach detection is replacing visual inspections to monitor riser sheath issues, and an externally mounted tool is making it possible to identify changes in applied stress in load bearing steel armoring wires. With this technology, unloaded armor wires can be identified at any location with +/- 15 m from the mounting location. Knowing the number of unloaded wires in a riser as well as the number of wires that can experience damage before there is danger of breakage, equipment can be operated longer and more safely.
Some regulatory agencies are now considering data gathered this way sufficient to provide knowledge necessary for authorizing operations to continue even where riser damage has been documented. The damage is being constantly monitored, so potentially serious issues can be identified and addressed immediately and swiftly.
Because risers normally are designed for a specific level of H2S or CO2, monitoring gas levels is also critical. A venting gas monitoring system that performs chemical analysis on permeated annulus gases in real time allows owners to identify changes in chemical concentration to mitigate riser damage.
Advanced solutions like these are valuable for aging assets, but they are equally useful in greenfield applications. Data show riser damage is common during installation and can impact service life. Inspecting risers during installation and continuously monitoring them from that point forward can improve operational safety and potentially increase the service life of the equipment.
What’s next?
Additional advances will soon enable real-time fatigue calculations using existing formulas and specially designed algorithms. In time, it will be possible to improve these models using historical performance data and applying lessons learned to deliver even greater improvements in riser integrity management.
Baker Hughes is exhibiting at booth E29 at ROG.e 2024 this week in Rio de Janeiro, Brazil.
About the Author
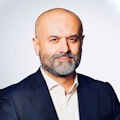
Domenico Di Giambattista
Domenico Di Giambattista is a seasoned energy executive who serves as vice president of flexible pipe systems at Baker Hughes, an energy technology company.
Di Giambattista has spent nearly 20 years in the oil and gas industry, leading product lines and regions around the world for Baker Hughes and GE Oil & Gas. In his current role, Di Giambattista oversees the design, manufacturing and installation of Baker Hughes’ flexible pipe systems and is based in Newcastle upon Tyne, England.
Di Giambattista earned a degree in mechanical engineering from Italy’s Università degli Studi dell'Aquila and a degree in project management from the Georgia Tech Scheller College of Business.